You can learn the recent information of Shijing.
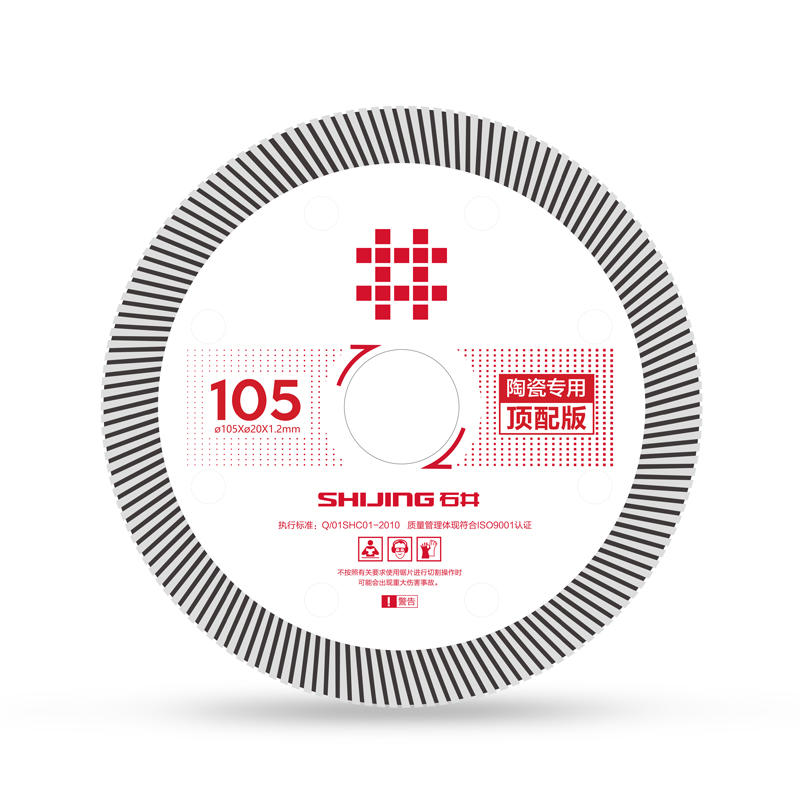
Wholesale cutting torch cart Tools Manufacturer
In the cutting tools industry, the quest for enhanced performance, durability, and efficiency has led to the development and adoption of advanced coating technologies. Among these, Physical Vapor Deposition (PVD) and Chemical Vapor Deposition (CVD) are two prominent techniques that significantly impact the performance of cutting tools. This article explores how PVD and CVD coatings improve the wear resistance and reduce friction of cutting tools, providing a comprehensive look at their benefits and applications.
Understanding PVD and CVD Coating Technologies
PVD is a vacuum coating process where materials are vaporized and then condensed onto the surface of cutting tools to form a thin, hard coating. This technology involves several methods, including sputtering and evaporation.
Sputtering: In sputtering, a target material is bombarded with ions, causing atoms to be ejected and deposited onto the cutting tool surface.
Evaporation: This process involves heating the coating material until it evaporates and then condenses on the cutting tool.
CVD is a process where gaseous precursors react at high temperatures to form a solid coating on the cutting tools. This method creates coatings with high hardness and nice adhesion.
Standard CVD: Involves using gases like methane or hydrogen to produce a coating on the tool surface through chemical reactions.
High-Pressure CVD: Operates at higher pressures, allowing for thicker and more uniform coatings.
Enhancing Wear Resistance
One of the primary benefits of both PVD and CVD coatings is their ability to significantly increase the hardness of cutting tools.
PVD Coatings: These coatings, such as titanium nitride (TiN) and titanium carbonitride (TiCN), are known for their exceptional hardness. The hard coating layer acts as a protective barrier, reducing the wear and tear on the cutting edge. This increased hardness allows cutting tools to maintain sharpness and precision over longer periods.
CVD Coatings: CVD coatings, like titanium carbide (TiC) and chromium carbide (CrC), offer high hardness levels. The thick, robust coating enhances the tool's ability to withstand abrasive wear and high temperatures during cutting operations.
The enhanced hardness provided by PVD and CVD coatings translates into a longer tool life.
PVD Coatings: By reducing the wear rate, PVD-coated cutting tools can operate for extended periods before requiring replacement. This durability translates to lower tool costs and reduced downtime for businesses.
CVD Coatings: The nice wear resistance of CVD coatings helps in maintaining tool performance and consistency. The extended tool life results in fewer tool changes and interruptions in production.
Reducing Friction
Coatings applied through PVD and CVD techniques contribute to a lower coefficient of friction between the cutting tool and the material being machined.
PVD Coatings: The smooth and hard surface of PVD coatings reduces friction, thereby smoother cutting actions and less heat generation. This is particularly beneficial when cutting difficult materials, as it minimizes the risk of tool sticking and reduces the force required for cutting.
CVD Coatings: CVD coatings provide a low-friction surface that helps in reducing the cutting forces. This not only enhances the efficiency of the cutting process but also decreases the amount of heat generated, which can be crucial for maintaining tool integrity and precision.
By reducing friction, PVD and CVD coatings contribute to a better surface finish on the workpieces.
PVD Coatings: The reduced friction allows for cleaner and more precise cuts, resulting in higher-quality surface finishes on the machined parts. This is important for applications where surface quality is critical.
CVD Coatings: The ability of CVD coatings to reduce friction leads to fewer defects and imperfections on the surface of the workpieces. This contributes to achieving the desired finish and tolerances in high-precision applications.
Applications and Benefits
In high-performance sectors such as aerospace and automotive manufacturing, where precision and durability are essential, PVD and CVD coatings offer substantial benefits.
PVD Coatings: These coatings are widely used for cutting tools that work with tough materials, such as aerospace alloys and automotive components. The increased hardness and reduced friction enhance the tool's performance and longevity, ensuring reliable operation under demanding conditions.
CVD Coatings: CVD coatings are employed for tools that need to endure bad temperatures and abrasive conditions. The robust nature of these coatings makes them suitable for applications involving high-speed cutting and heavy-duty machining.
In general manufacturing, the use of coated cutting tools can thereby significant improvements in production efficiency and cost-effectiveness.
PVD Coatings: The versatility of PVD coatings allows them to be applied to various cutting tools, including drills, mills, and taps. This versatility helps manufacturers achieve better performance and longer tool life across a wide range of machining operations.
CVD Coatings: The durability of CVD coatings makes them ideal for applications involving hard or abrasive materials. Their ability to maintain performance over extended periods reduces the frequency of tool changes and enhances overall productivity.
The application of PVD and CVD coating technologies has profoundly impacted the performance of cutting tools, offering significant improvements in wear resistance and friction reduction. By enhancing the hardness of the cutting edge and lowering the coefficient of friction, these coatings contribute to extended tool life, improved surface finish, and increased efficiency in machining operations. As the cutting tools industry continues to evolve, the ongoing development and refinement of coating technologies will play a crucial role in meeting the growing demands for precision, durability, and performance.