You can learn the recent information of Shijing.
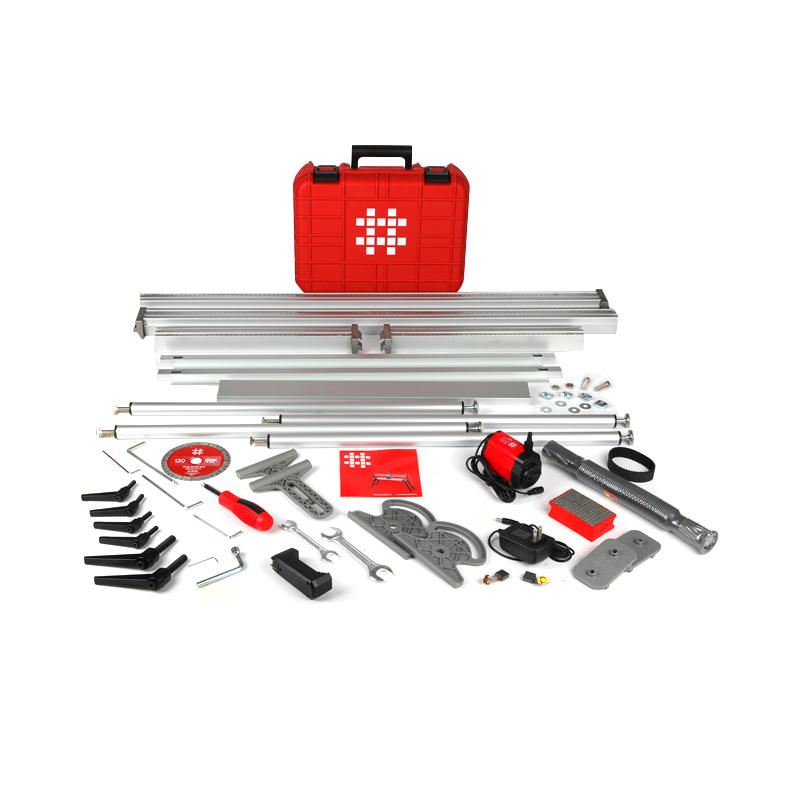
OEM gear cutting tools Factory
In the competitive landscape of manufacturing and industrial production, the choice of cutting tools can significantly impact a company's bottom line. Cutting tools are essential for various applications, from metalworking to woodworking, and their efficiency directly influences the productivity and quality of the end product. This article aims to provide an in-depth analysis of the investment return on different types of cutting tools, considering both initial costs and long-term usage expenses.
The cutting tools market is a dynamic sector that encompasses a wide range of products, from simple hand tools to sophisticated computer numerical control (CNC) machine tools. The selection of the right cutting tool is crucial for achieving precision, efficiency, and cost-effectiveness in any manufacturing process. Cutting tools can be broadly categorized into several types, including:
Known for their versatility and affordability, HSS tools are a popular choice for general-purpose cutting applications.
These tools offer greater hardness and wear resistance compared to HSS, making them suitable for harder materials and higher cutting speeds.
With their high-temperature resistance, ceramic tools are ideal for cutting materials at high speeds without losing their edge.
These tools are used for cutting extremely hard materials, such as ceramics and hard metals, where other tools would fail.
CBN tools are designed for machining hard ferrous materials, offering advance performance in terms of tool life and cutting speed.
When evaluating the initial cost of cutting tools, it's essential to consider the material, manufacturing process, and the complexity of the tool's design. High-speed steel tools are generally the more cost-effective option, making them an attractive choice for small-scale operations or for applications where tool life is not a critical factor. On the other hand, carbide, ceramic, diamond, and CBN cutting tools come with a higher initial cost due to the expensive materials and advanced manufacturing processes involved.
While the initial cost is a significant factor, the long-term usage costs of cutting tools are equally important. These costs include tool life, maintenance, downtime, and the quality of the cut. Carbide, ceramic, diamond, and CBN cutting tools, despite their higher initial cost, often provide a better return on investment due to their longer tool life and ability to maintain a sharp edge under demanding conditions.
The lifespan of a cutting tool is a critical factor in determining its long-term cost-effectiveness. High-quality cutting tools like carbide, ceramic, diamond, and CBN can last significantly longer than HSS tools, reducing the frequency of tool changes and minimizing downtime. Additionally, these tools often require less frequent sharpening or reconditioning, which can save on maintenance costs.
Downtime due to tool changes or tool failure can be costly, especially in high-volume production environments. Cutting tools with a longer tool life, such as carbide, ceramic, diamond, and CBN, can help minimize downtime by reducing the need for frequent tool changes. This, in turn, can thereby increased productivity and a higher output of finished products.
The quality of the cut is another factor that influences the return on investment of cutting tools. High-quality cuts can reduce the need for secondary finishing processes, saving both time and money. Cutting tools made from advanced materials like carbide, ceramic, diamond, and CBN often provide nice cutting performance, resulting in cleaner, more precise cuts that require less post-processing.
In conclusion, while the initial cost of cutting tools can vary widely, the long-term return on investment should be the primary consideration for manufacturers. High-quality cutting tools, such as carbide, ceramic, diamond, and CBN, may require a higher upfront investment but can offer significant savings in the long run through reduced downtime, lower maintenance costs, and improved cut quality. By carefully analyzing the specific needs of their production processes and the characteristics of different cutting tools, manufacturers can make informed decisions that optimize their investment and enhance their overall productivity.