You can learn the recent information of Shijing.
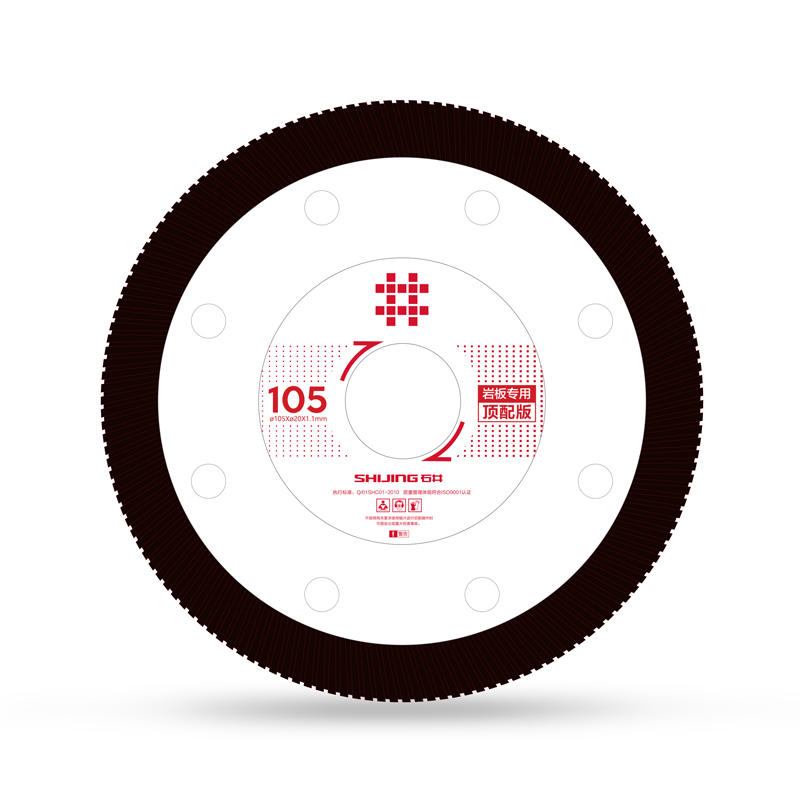
Direct Selling OEM/ODM cutting tools Company
In the intricate realm of manufacturing and craftsmanship, OEM/ODM cutting tools stand as unsung heroes, orchestrating the delicate ballet of transforming raw materials into refined masterpieces. These instruments, often underestimated in their significance, play a pivotal role in shaping diverse industries such as automotive, aerospace, and construction. In this exploration, we delve into the artistry and functionality of OEM/ODM cutting tools, unraveling their nuanced dance on the stage of material manipulation.
The Symphony of Precision
At the heart of any cutting tool is an amalgamation of precision and engineering finesse. These instruments, ranging from simple hand tools to sophisticated computer-numerical-control (CNC) machines, execute a symphony of meticulously calculated movements. Each cut is a choreographed performance, where the cutting tool encounters the material with finesse, guided by the hand of skilled operators or the algorithms of advanced software.
The Dance Partners: Materials and OEM/ODM cutting tools
In this grand performance, the materials being worked upon serve as the silent dance partners to the OEM/ODM cutting tools. Metals, plastics, and composites, each with its unique set of challenges, engage in a tango of transformation. The cutting tools, armed with various geometries and coatings, navigate this intricate dance floor, ensuring precision and efficiency.
The Ballet of Geometry
One of the fundamental aspects defining the efficacy of OEM/ODM cutting tools is their geometry. The interplay of angles, curves, and edges determines how the tool interacts with the material. For instance, the rake angle influences the cutting force and chip formation, while the clearance angle dictates the tool's ability to evacuate chips. The dance of geometry is not merely an aesthetic consideration; it is a crucial determinant of the tool's performance and longevity.
Tool Materials: Crafting the Performers
Just as a dancer requires the right shoes, OEM/ODM cutting tools demand materials of exceptional quality. High-speed steel (HSS), carbide, and ceramics emerged as the prima ballerinas of the cutting tool world. Each material brings its unique strengths to the stage, with HSS exhibiting toughness, carbide showcasing hardness, and ceramics delivering high-temperature resistance. The choice of material influences the tool's durability and its ability to withstand the rigors of the machining dance.
The Choreography of Coatings
In the intricate choreography of material removal, coatings emerge as the elegant embellishments on the cutting tool's attire. Titanium nitride, diamond-like carbon, and various ceramic coatings don the tools, enhancing their performance and extending their lifespan. These coatings reduce friction, dissipate heat, and, in some cases, add a layer of chemical resistance, contributing to the overall finesse of the cutting process.
The Maestros: Skilled Operators and CNC Precision
Behind every successful performance of cutting tools, there is a maestro—be it a skilled machinist or a computerized numerical control (CNC) system. The skilled operator interprets the nuances of the material and adjusts the cutting parameters, ensuring a harmonious interaction between the tool and the workpiece. On the other hand, CNC systems execute pre-programmed choreography with robotic precision, turning the machining process into a mesmerizing ballet of automation.
Adaptability: A Virtuoso Trait
The realm of OEM/ODM cutting tools is not stagnant; it's a dynamic landscape that demands adaptability. From traditional lathe tools to modern multi-axis CNC machines, cutting tools evolve to meet the demands of emerging technologies and materials. The ability to adapt, much like a dancer adjusting to different styles, defines the longevity and relevance of cutting tools in the ever-changing world of manufacturing.
Economic Impact: Cutting Tools as Economic Catalysts
Beyond the workshop floor, OEM/ODM cutting tools wield substantial economic influence. The efficiency and precision they bring to manufacturing processes ripple through the entire supply chain, reducing waste, optimizing production, and ultimately contributing to cost-effectiveness. The economic impact of cutting tools extends beyond individual industries, affecting national and global economies as they propel innovation and productivity.
Conclusion
As technology advances and materials evolve, OEM/ODM cutting tools continue to evolve, embracing new challenges and shaping the future of production. So, the next time you witness the symphony of a CNC machine or the elegance of a lathe in action, remember the unsung heroes—the cutting tools—that make the dance of material transformation possible.